Energy Management
Total Energy Consumption
Note:
- Intensities are calculated based on overall production including inter-company sales.
- 2020 energy has increased as Indorama Ventures acquired cracker plants, which resulted in higher energy consumption.
- 2020 and 2021 environmental data has been restated using a more stringent definition and methodology.
- 2020 baseline was adjusted for an alignment.
2025 target:
Nitrogen oxides (NOx), sulfur oxides (SOx) and other significant air emissions (ton) | 2021 | 2022 | 2023 | 2024 |
---|---|---|---|---|
Total NOx emissions | 12,433 | 7,536 | 7,448 | 7,019 |
Total SOx emissions | 6,999 | 5,730 | 5,708 | 3,854 |
Total VOC emissions | 2,364 | 4,287 | 3,253 | 3,360 |
Total PM emissions | 915 | 1,137 | 1,217 | 1,283 |
In 2024, Petform (Thailand) Limited – Lopburi implemented an energy efficiency improvement project by upgrading its preform injection mold from a 48-cavity to a 72-cavity configuration. By increasing the number of cavities per mold, we were able to produce more preforms per injection cycle, thereby reducing overall energy consumption per unit produced. This modification resulted in a 15% reduction in energy use compared to the previous 48-cavity setup. In addition to enhancing production efficiency, the project delivered annual cost savings of over THB 370,000. This initiative highlights our commitment to reducing energy consumption through process optimization and operational improvements.
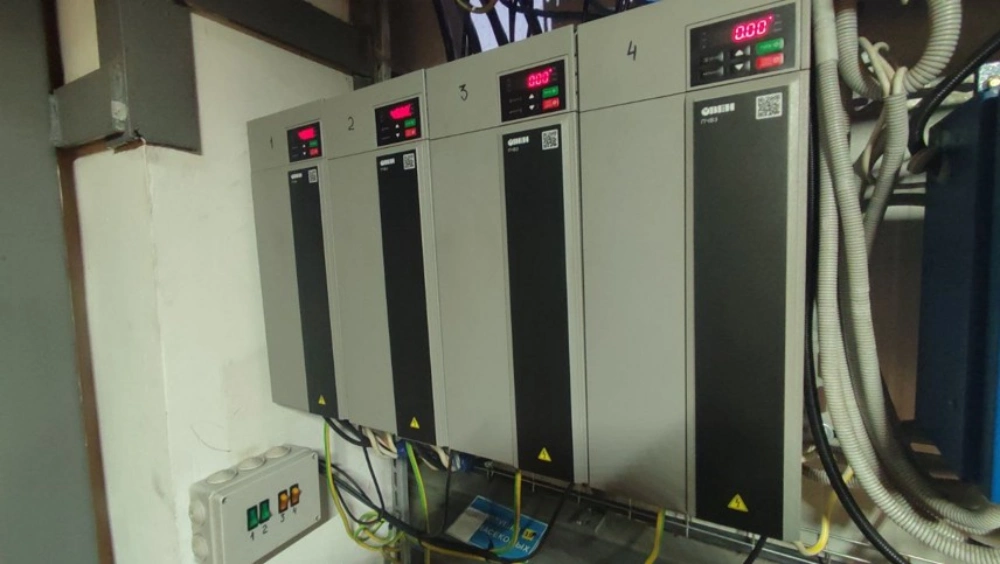
In 2024, Avgol Russia improved energy efficiency by installing Vector Frequency Converters (VFCs) on electric motors in its ventilation system, replacing fixed-speed magnetic starters. This upgrade enabled dynamic motor speed control based on seasonal and operational needs. As a result, the project achieved annual energy savings of 1,020 MWh, reduced GHG emissions by 370.95 tCO₂, and generated cost savings of $62,000 per year.
Moreover, the ability to adjust motor speeds lowered the demand on the heating system, leading to a reduction in natural gas consumption. This initiative showcases scalable energy optimization and operational efficiency, while also reducing the use of non-renewable energy sources.
Indovinya aims to capture ethylene lost in the demethanizer tower that typically goes into fuel gas. The impact will be a reduction in the overhead temperature of the demethanizer by installing a two-stage turbo-expander and a new cold box to recover incremental ethylene. Energy is saved both from the recovery of ethylene from the residue gas stream and from unloading the refrigeration system. This results in significant energy savings: 158,227 MMBtu/year from recovered ethylene and 287,376 MMBTU/year from unloading propylene refrigeration. Cumulatively, the project reduces energy consumption by 445,603 MMBtu/year and lowers CO2 emissions by 23,661 tons/year.
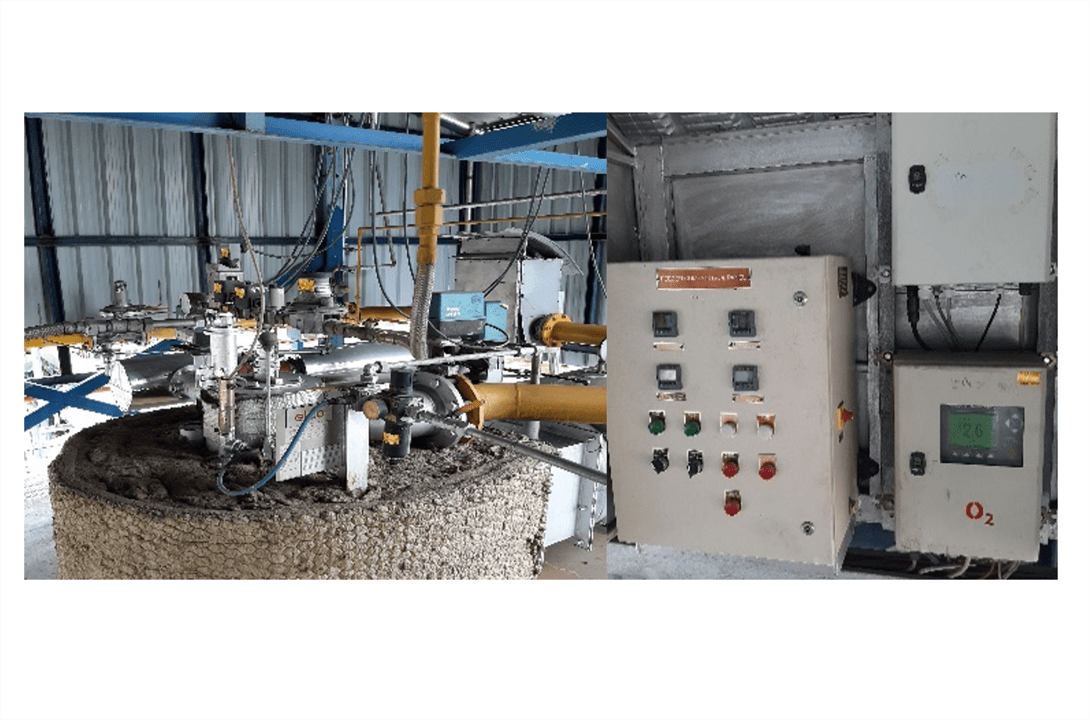
To minimize the generation of air pollutants from our operations, Indorama Polyester Industries (Rayong) has implemented air pollution control measures that go beyond legal requirements. The company has switched the fuel used in the dowtherm boiler from coal to natural gas and installed a CO control system, which enhances combustion stability. As a result, in 2024, our NOx emissions were 27 tons per year, which is below our target of not exceeding 35.23 tons per year. Additionally, the NOx emissions are 43% lower than the standards set by the EIA. This achievement underscores our commitment to environmental stewardship and reflects our proactive efforts to improve air quality beyond the regulatory standards.
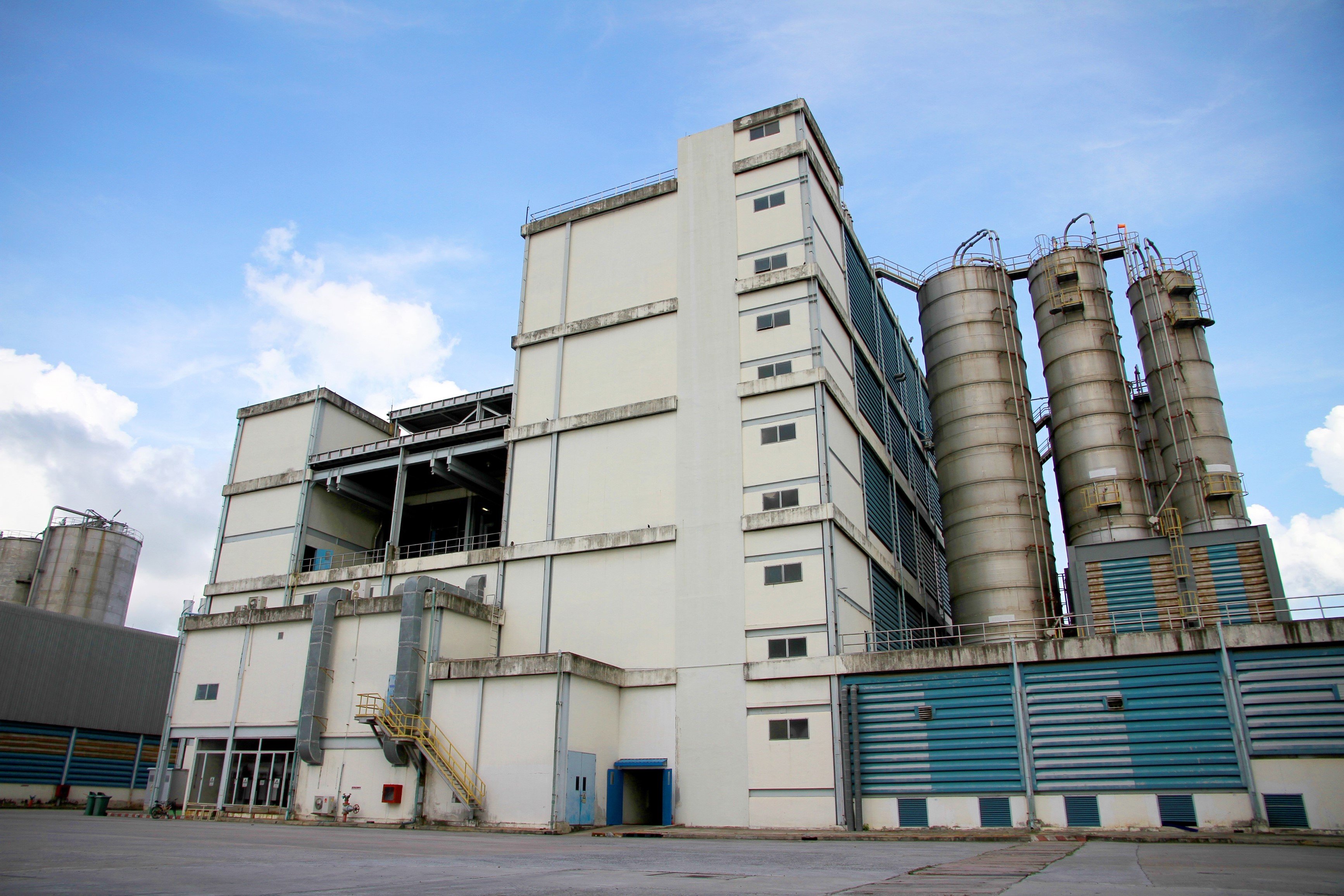
To support our ambition to reduce fossil fuel usage and GHG emissions, Indorama Petrochem Limited (PET), Thailand, has been transitioning from natural gas to biomass for its heaters since 2017. The designed heaters can utilize various biomass materials, including wood chips, wood pellets, and palm kernel shells. In 2023, we expanded our biomass heating capacity with the installation of Biomass Heater C, which has a capacity of 14 MW. Biomass Heater C will be fully operational in 2024, enabling us to reduce GHG emissions by an estimated 9,733 tCO2e per year and replace approximately 38,131 tons of natural gas with biomass annually.
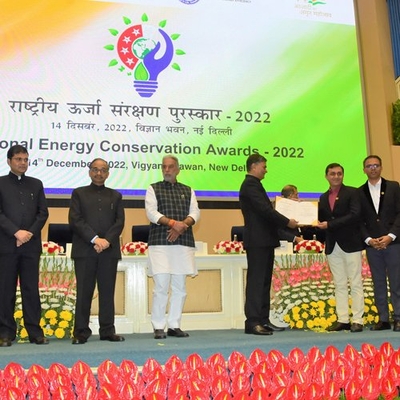
Indorama Ventures Oxides Ankleshwar Pvt Ltd (IVOAPL) has achieved a significant reduction in GHG emissions and energy use through various onsite energy savings initiatives by its Utility and Engineering teams. These initiatives resulted in a reduction of 585 tCO2e/year in GHG emissions and a decrease in energy consumption by 2,345 GJ/year. The company’s commitment to reducing energy use and improving operational efficiency was acknowledged at the National Energy Conservation Awards 2022, further supporting Indorama Ventures’s Vision 2030 to become a global sustainable chemical company.
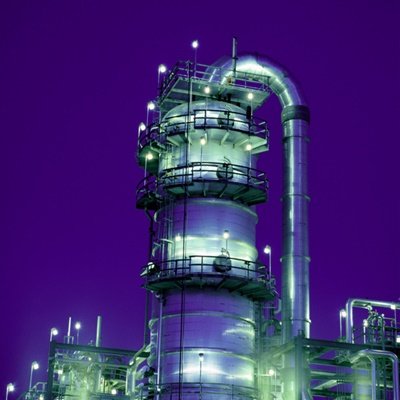
The IVOX Port Neches Team carried out studies to determine the impacts of bypassing the Propylene Recycle tower, by sending a portion of the propylene stream to the olefins unit tower for processing, with the remainder sent for recycling to Epoxidation. This project is expected to yield an energy reduction of 324,090 GJ/year along with an emissions reduction of 478 metric tons of CO2. The process efficiencies achieved from this project would lead for a total operational savings of US$ 2.6 million.
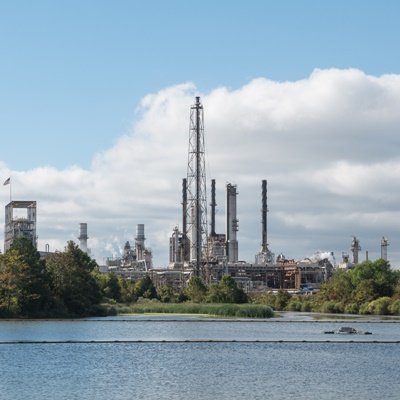
Beyond Compliance: Guangdong Indorama Ventures PET Polymer Kaiping Limited, our wholly-owned subsidiary in China, has undertaken environmentally-friendly initiatives installing a nitrogen oxide (NOx) reduction system valued at over USD 230,000 to reduce NOx values beyond limits permitted by the government. This initiative has resulted in environmental, social and economic benefits which include:
- Less NOx emissions in the air, much lower than permitted levels.
- No solid or liquid contaminant is being generated or secondary pollution during operations.
- Low running costs due to use of less expensive catalysts.
- Easy to handle, transport and store as the new reducing agent is uninflammable and non-explosive.
Indorama Petrochem Limited (PET)’s plant in Rayong, Thailand, continues to demonstrate strong stakeholder engagement and significant process optimizations. At the end of 2019, the plant installed a stripping column to reduce the COD/BOD in wastewater prior to its delivery to a wastewater treatment plant. In addition, a catalytic incinerator was installed to remove any off-gas from the process. In 2020, electrostatic precipitators (ESPs) were used to replace the cyclonic separation process for particulate collection. This initiative reduced total suspended particulates by 91% and reduced the NOx emissions rate by 29%. These actions demonstrate Indorama Ventures’s solutions that meet or exceed stakeholder expectations.
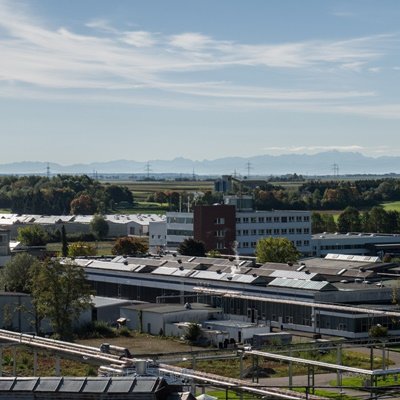
Optimizing our systems to reduce carbon emissions and energy consumption is integral to reaching our 5% energy intensity reduction by 2025. In support of these reductions, our Trevira Bobingen site in Germany has been utilizing waste heat exchangers. Heat generated by air compressors is recycled and used within the manufacturing process to preheat boiler feed water and finish dip baths. In 2020, This technology achieved an energy saving around 23,740 GJ and reduced carbon emissions of 1,360 tCO2e.