Waste Management
We are committed to reducing our waste through our continued focus on improving operational eco-efficiencies and higher resource utilization. We ensure that strong compliance standards are in place to manage the waste at our sites according to regulatory requirements. This includes proper waste inventory by name, type, code (as required by law), storage location, method of offsite transportation, treatment and disposal, quantity of waste generated, and waste stored onsite and disposed of both onsite and offsite. We also ensure that our waste is disposed through sustainable and qualified vendors who reuse, recover or recycle. We manage our waste responsibly, strive to exceed regulatory requirements, and record the quantity of waste generated, stored onsite, and disposed of onsite and offsite. In addition, we carry out site audits of key vendors to ensure that their waste management standards are in-line with approved local regulations in addition to our sustainable practices.
Target:
Actual:
2025 target:
Total Hazardous Waste
Total Waste
Generated, Disposed, Reused, Recycled and Recovered
Unit | 2021 | 2022 | 2023 | 2024 | |
---|---|---|---|---|---|
Total non-hazardous waste generated | Tons | 287,069 | 307,901 | 315,007 | 326,780 |
Total non-hazardous waste reused, recycled and incinerated (with and without energy recovery) | Tons | 181,992 | 76,074 | 87,292 | 112,821 |
Total non-hazardous waste disposed (composed, landfill, deep-well injection and others) | Tons | 105,076 | 231,827 | 227,715 | 213,959 |
Note:
- Intensities are calculated based on overall production including inter-company sales.
- 2021 environmental data has been restated using a more stringent definition and methodology.
- Waste diverted from landfill includes waste that is incinerated with energy recovery.
Indorama Ventures Mobility Puebla IVMP partnered voluntarily with state-authorized recyclers to divert cardboard and wood waste from landfills. Launched in November 2023, this cross-functional initiative aligned waste management procedures with state requirements and supported certification for key buyers.
On 15 April 2024 we received our first certificate, recognizing the collection of 91,444 kg of cardboard and wood waste. This effort preserved 5,374 mature trees, as certified by the Sustainability Office of the State of Puebla’s Certificate of Collection, Transportation, and Final Disposal of Common Solid Waste. The preservation of these trees enables the annual absorption of 145,098 kg of CO2, showcasing our steadfast commitment to environmental compliance, circularity, and the responsible stewardship of natural resources.
Petform (Thailand) Limited – Lopburi launched a waste reduction initiative by reusing film cores that were likely to end up in landfill. Through internal collaboration, the team established reuse procedures, revised related documentation, and communicated with customers to ensure compatibility with the updated process. This approach allowed us to reuse film cores effectively and reduce the volume of waste generated. In 2024, the project achieved an average reduction of 49.51% in film core waste, surpassing the original 20% target. This initiative demonstrates our effort to divert waste from landfill and support circular resource management by extending the useful life of packaging components.
In 2024, Indorama Ventures Sustainable Solutions Brazil implemented a waste reduction initiative in the rPET production line by minimizing “good flakes” in the metal reject stream, aiming to reduce losses from 6.5% to 0.5%. The team addressed this issue by adjusting detector sensitivity, enhancing cleaning routines, conducting loss audits, and installing magnetic grids. As a result, flake losses dropped to 0.98% within six months, leading to an average savings of 75 tons of flake per quarter and an estimated annual cost savings of $ 135,000.
This initiative represents a process improvement effort aimed at minimizing production waste, which not only enhances resource efficiency but also maximizes material yield, reduces environmental impact, and supports a more circular production process.
In 2023, Indorama Ventures Mobility Scottsboro launched a project to improve the quality of Nylon 66 yarn products, specifically focusing on SDW (Spinning, Drawing, Winding) A Grade. This initiative involved optimizing process profile settings (including extruder temperature and draw field settings), reducing downtime caused by breakouts, and addressing equipment issues. Consequently, productivity will increase from 81.7% to 88.6%, resulting in cost savings of approximately $755,000 per year. This initiative will not only enhance overall operational efficiency but also significantly reduce production waste, such as C-grade products, leading to a more efficient use of resources.
Indorama Polyester Industries (Rayong) has been continuously implementing a zero waste to landfill program since 2021. One of the methods we use to manage waste is by sending production waste, including off-grade products from the fiber production process such as polymer waste, POY waste, and fiber waste, to legally certified companies. These companies will use the waste as raw materials for further fiber production. In 2024, the site sent 2,480,729 kg of production waste to certified companies for recycling and reuse as raw materials. All of the waste was successfully repurposed, achieving a 100% reuse rate. This initiative significantly reduces landfill contributions, promotes circular resource use, and enhances the site's environmental performance.
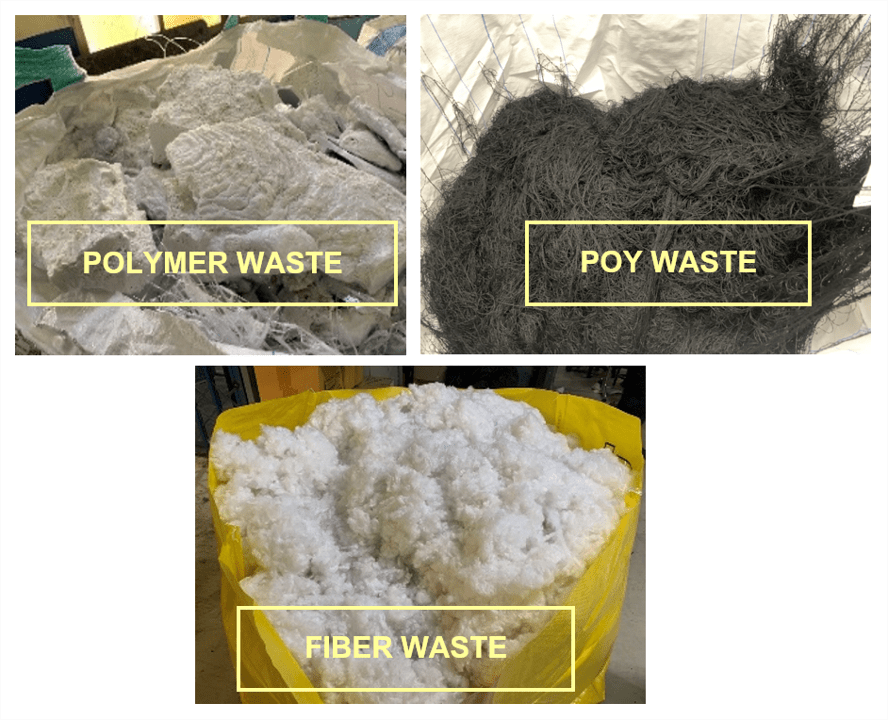
In 2024, Petform (Thailand) Limited - Lopburi implemented a project to reduce hazardous waste generated during machinery maintenance. The project involved revising maintenance plans and procedures to prevent hydraulic oil leaks and reduce the use of rags, which become contaminated materials that require disposal. Additionally, training sessions were conducted to educate employees on operational methods and waste management, raising awareness about waste reduction and improving operational practices. As a result of these initiatives, we successfully reduced contaminated rag waste by 22% and decreased the volume of oil sent for disposal by 34%, compared to the levels generated during machinery maintenance in 2023. These efforts also led to a cost saving of over 83,000 THB in waste disposal for oil and rags.
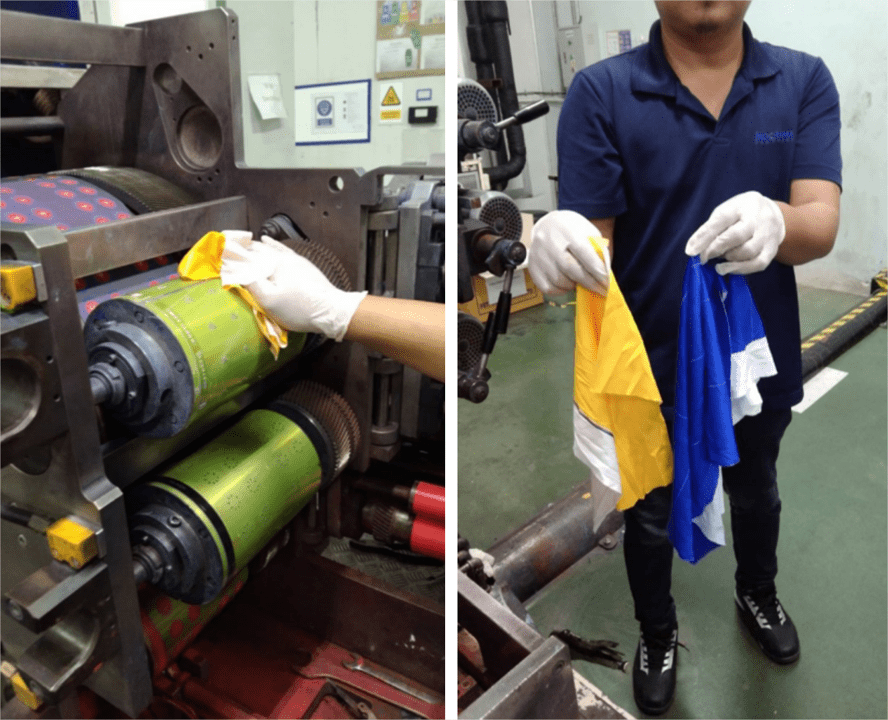
Indorama Synthetics (India) has successfully implemented an automatic chemical dosing system for two of their cooling towers. This represents a significant advancement in automation and digitization, and offers numerous advantages over manual dosing. The automated system ensures that the desired level of chemicals is consistently maintained in the system, preventing both corrosion and scaling caused by underfeeding, in addition to chemical waste due to overfeeding.
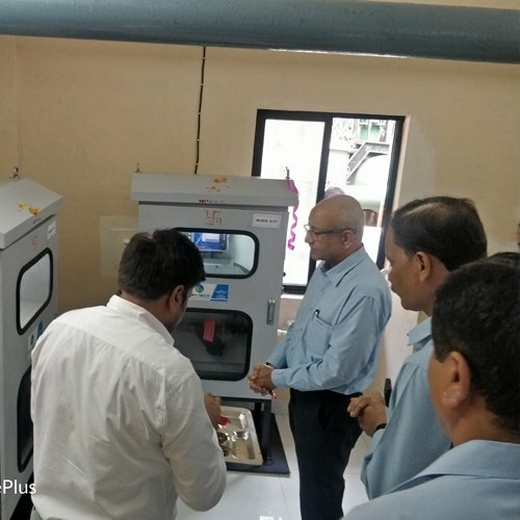
Performance Fibers (China)
Indorama Ventures fully supports China’s policy of reducing emissions and increasing energy efficiency while promoting technological progress. This is also integral in achieving our sustainability goals which are aligned with our vision: To be a world-class sustainable chemical company making great products for society.
Our Performance Fibers subsidiary in China focused on improving resource efficiency and reducing chemical waste. The chemical waste produced from tire cords consists of a complex structure, does not biodegrade easily and carries high treatment costs. the division initiated a project to reduce chemical consumption in its production process.
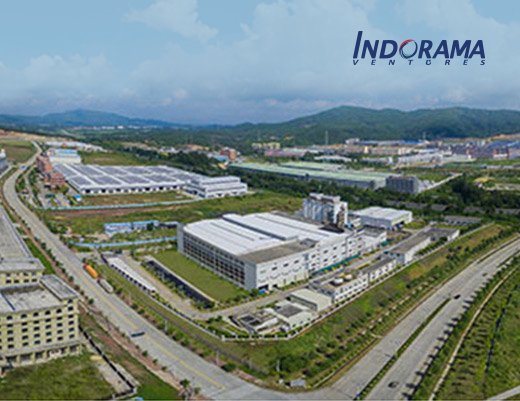