Health and Safety
Environmental, Health & Safety Commitment & Policy
IVL is committed to providing a healthy environment and a safe workplace for all staff through a combination of interactive consultations from all of its employee groups. This helps to identify and implement the measures needed to achieve our target of injury-free workplaces and process safety. We use a risk-based approach to identify concerned staff who may require assistance in stress management in addition to adopting ergonomic improvements at workstations to provide an environment that relieves stress and increases productivity for everyone. We are working with the Joint Action Committee of employees to ensure that all levels of our workforce are in statutory compliance, taking account of compulsory and periodic Health & Safety Training while equipping all staff with Personal Protective Equipment (PPE) in-line with their responsibilities. We are determined to maintain zero fatalities in our operations and to continually improve our performance in health, safety and well-being through certification of the ISO 45001/OSHAS 18001 management system, internal corporate standards.
Health, safety and well-being represent our core values. Indorama Ventures PCL. continuously implements programs for improvements and places the health and safety of our workforce at the forefront of our activities. We respect and support collective bargaining agreements that address employees’ health and safety, working conditions, and other workplace-related considerations. Management discussions on health and safety issues with worker representatives is regularly conducted to ensure the alignment on direction and actions towards the healthy and safety environment and culture. This enhances our appeal as an employer of choice, promotes employee satisfaction and productivity, and ensures that we continue to attract and retain a capable workforce.
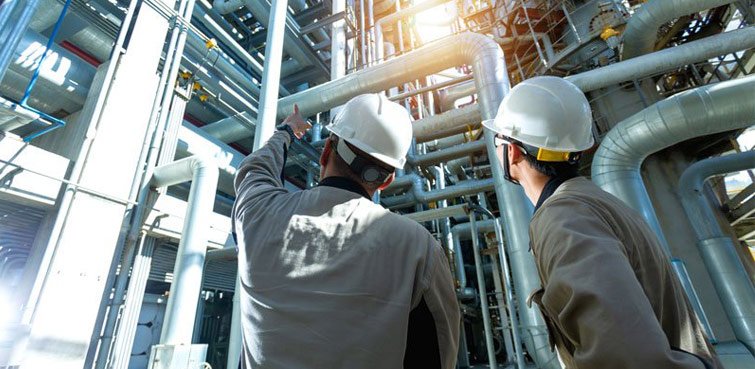
Placing the EHS function at the core of the business provides continuity, realizes efficiencies and allows us to achieve synergies with other enabling functions such as Sustainability and Business Continuity. The EHS function also allows for stronger central steering, increased expertise and is integral to achieving our sustainability vision.
EHS's core accountabilities
Governance and Standardization
- Standardize practices across process safety, environmental compliance, occupational health & hygiene, and safety.
- Define systems, a common methodology and drive the use of software solutions to facilitate the execution and monitoring of compliance with IVL standards.
Assurance
- Develop, deploy and monitor EHS KPIs to maintain a company-wide overview.
- Deploy EHS programs such as Injury & Illness Prevention Program (I2P2) and establishing the Golden Rules to drive improvements.
- Design audit systems and EHS maturity scorecards.
- Evaluate regulatory compliance, adherence to IVL EHS standards at sites, and transparent reporting to management through monitoring our defined metrics.
Building EHS Capabilities
- Strive for high standards of EHS performance from all employees.
- Investment in the EHS capabilities, such as founding the EHS Academy.
- Create opportunities, such as global audit team member participation, networking and serving on Communities of Practice (COP).
Innovation
- Collaborate with cross-functional teams to identify and implement, when appropriate, new EHS-related technologies and processes.
- Staying up to date with industry trends and emerging technologies, effectively communicating these advancements to relevant stakeholders, and fostering a culture of continuous improvement.
- Leveraging data and analytics to enhance efficiency, reliability, and technological innovation in EHS practices across Indorama Ventures.
Health and Safety Management System
As demands increase for improved Health, Safety and Well-being, our adoption of a risk-based approach was a key strategic move taking into account all areas of risk including legislative requirements, the capacity of our employees, and the potential hazards from our manufacturing activities. As part of this process, we carried out numerous simulations and scenarios on health and safety to identify key areas of concern to improve our performance. The goal is to implement more appropriate measures which we can implement throughout our global network.
We continue to expand the implementation of occupational health and safety management systems across our sites, with more plants obtaining ISO 45001:2018 or OHSAS 18001:2007 certification over time. To support this, annual audits performed by professional third parties are scheduled periodically, allowing auditors to critically evaluate the strengths and weaknesses of our OH&S system. The plant manager, together with relevant OH&S staff, are proactive in addressing any observations regarding gaps or areas for improvement raised by the auditor. Their recommendations are conveyed to senior management.
Golden Safety Rules
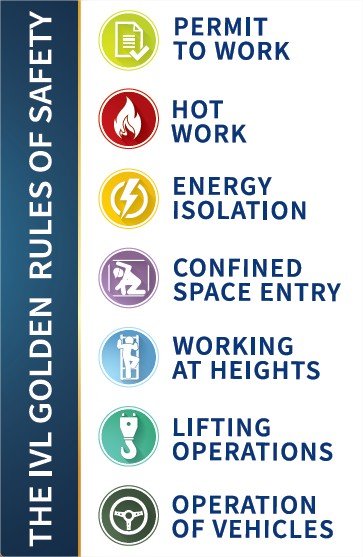
IVL has implemented the Golden Safety Rules. These rules provide support for key life-critical activities. They are for all personnel (employees or contractors) working at IVL operated sites who carry out, or are responsible for, activities with particular potential to cause serious injuries or incidents, especially fatalities.
The Golden Safety Rules demand our full attention and are considered of utmost importance when it comes to protecting people. Each rule in the handbook outlines IVL’s minimum requirements and is accompanied by a detailed corporate standard.
Local sites are responsible for developing systems and conditions that align with IVL’s corporate rules, as well as training employees to understand them.
EHS Excellence Awards
We believe that recognizing superior EHS performance and valuable contributions from our team members worldwide is a key element to building a positive EHS culture. 2021 was the inaugural year for IVL’s EHS Excellence awards. The EHS Excellence Award are awarded to an individual or team (EHS or non-EHS) that has demonstrated a conscious effort to reduce risk, drive improvements in safety or environmental programs, lead others to do the same, or otherwise champion a strong safety or environmental compliance culture. In 2023, 9 site performance awards were given and 10 individual or team awards were given (or 19 awards from 124 nominations were given).
EHS software solutions
IVL is implementing various software systems to streamline data collection for EHS metrics and allow better oversight of risks company-wide. These systems are used for incident management, action tracking, compliance tracking and regulatory registers, auditing and health data management. This allows us to track not only lagging indicators such as TRIR and LTIFR but also leading indicators such as open incident investigations, actions related to investigations or audits, compliance tasks, overdue investigations, actions, or compliance tasks.
Health and Safety Performance
IVL’s Corporate EHS Structure consists of the Center of Excellence (COE) and Regional Directors that work closely with EHS Business Heads, Site EHS Heads and local EHS professionals. The COE has experts on Industrial Hygiene, Occupational Health, Occupational Safety, Process Safety, Environmental Management and EHS Data Analysis. The COE is responsible for EHS Governance (company-wide EHS standards). The Regional Directors cover the three regions of the Americas, Europe-Middle East-Africa and Asia-Pacific. Regional Directors coordinate and ensure sharing best practices within their region but are also responsible for IVL’s auditing program. EHS Business Heads are responsible for driving EHS and sharing best practices within their segment. Site EHS Heads and local professionals are responsible for ensuring their site’s compliance with corporate standards and local regulations.
Lost Time Injury Frequency Rate: LTIFR (cases/Million man-hours) | 2021 | 2022 | 2023 | 2024 |
---|---|---|---|---|
Employees | 4.05 | 3.30 | 3.02 | 2.15 |
Contractors | 1.22 | 0.80 | 1.12 | 1.55 |
Fatalities (Person) | 2021 | 2022 | 2023 | 2024 |
---|---|---|---|---|
Employees | 1 | 0 | 0 | 1 |
Contractors | 1 | 1 | 3 | 3 |
Comparing our global employee injury/illness rate (TRIR) to that of our peer member companies in the American Chemistry Council, Indovinya, our subsidiary of Indorama Ventures, finished the year 2023 in the 1st quartile, and for process safety performance globally, we are in the 2nd quartile. We realized a 29% decrease in environmental permit exceedances.
Area of Expertise
Facility, Process and Occupational Safety
We work diligently to meet or exceed multiple applicable industry and corporate level standards to provide a safe working environment for our workers and neighbors. This includes meeting the requirements of each element of the OSHA Process Safety Management (PSM) 1910.119 standard, and the requirements of multiple ISO standards, such as ISO-9001 (Quality Management Systems), ISO-14001 (Environmental Management Systems), ISO-45001 (Occupational Health and Safety), and ISO-50001 (Energy Management Systems).
With these standards in place, we are prioritizing our workforce safety, we are continuously enhancing our training programs to improve our workers’ skills and safety awareness, we have established a set of Golden Safety Rules that are at the highest priority of every facility, we are ensuring that our plant’s infrastructure and equipment are properly maintained, and we are using the information learned to invest in enhancing our safety performance to reduce the risk of safety incidents and to improve our efficiencies.
Each IVL facility is tasked with assuring that clear responsibilities are defined and in place as part of the overall facility safety management. Facility personnel conduct risk assessments commensurate with the respective risk of the task and process operation and ensure that all IVL incidents and associated actions are entered into a common software platform for the recording of investigations and the proper management of actions.
Health Programs
Environmental Programs
Practices
Lighting, Noise and Indoor Air Quality
Ergonomic Workstations
Voluntary Health Practices
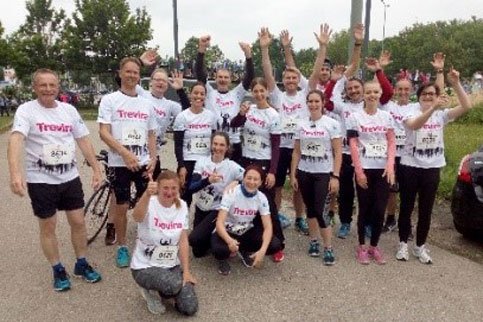
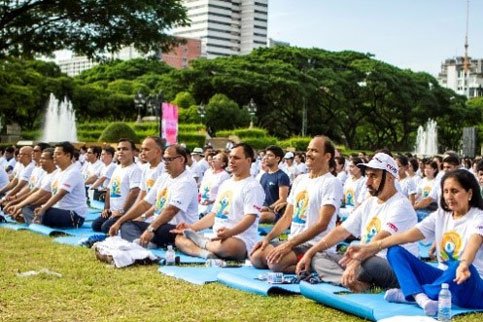
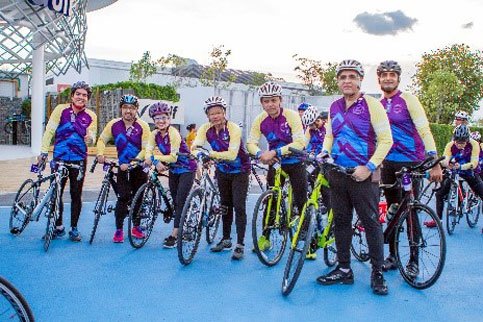
Training and Protective Personnel Equipment (PPE)
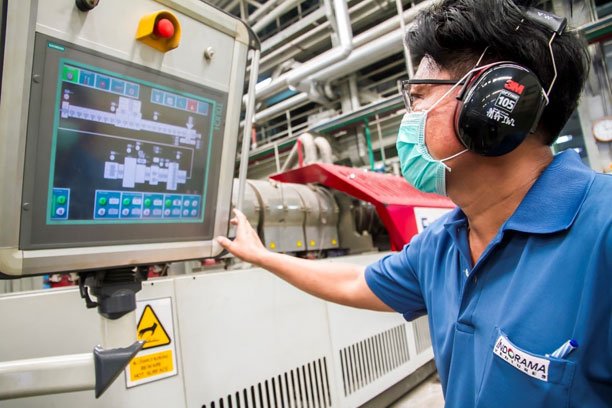
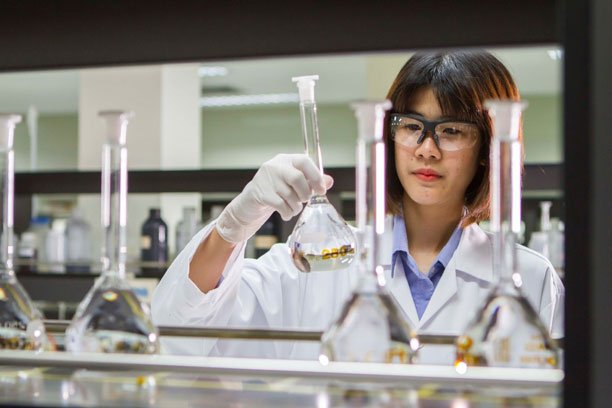
Health & Safety Management System (ISO 45001/OHSAS 18001)
Results
Goal of no harm
Engaging workers through consultation, communication, and collaborative processes are important ways to achieve our target of zero fatalities. Discussions on safety, including near-miss incidents, raised by on-the-ground staff are periodically conducted to provide lessons learned, and to establish a practical response. This is then circulated among relevant employees to prevent reoccurrences. Increased awareness and achieving continuous improvements is the key to zero fatal, zero accident and safe work environment. As EHS incidents are reported, the level of severity is determined, and management reviews are conducted according to the severity of the incident. Investigation rigor is determined according to the severity level and potential. Lessons learned and best practices are consistently shared throughout IVL to continuously improve together. The conclusions are shared with other entities.
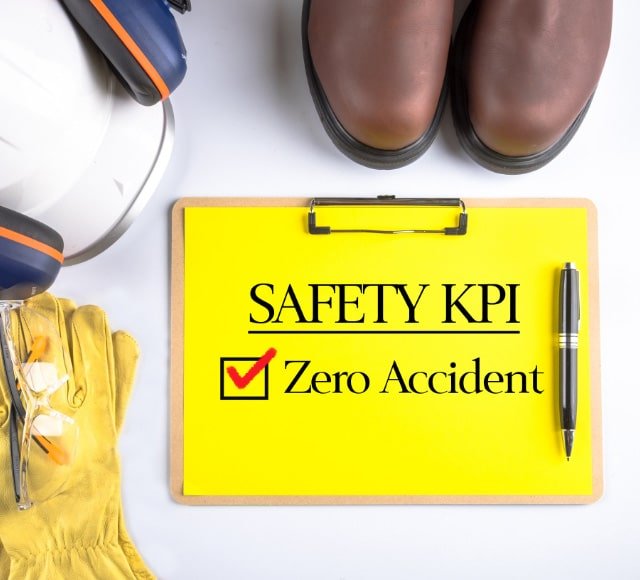
Monitoring performance to encourage continuous reduction of injuries, illnesses, process safety and environmental events
Any injury or occupational disease is carefully handled by the supervisor and related OH&S staff. All IVL plants around the world have established various measurable indicators that cover total recordable injuries, total lost time, the number of lost days, and the number of absentee days, etc. These indicators are monitored on a routine basis, then the root cause is identified including any possible factors that trigger the incidents. All of the indicators and accompanying data are centralized, consolidated and presented to the Sustainability and Risk Management Committee (SRMC) annually ensuring that any injuries or occupational disease that occur in the workplace are discussed resulting in more robust actions that reduce the rate of injury/occupational disease. The root cause analysis, relevant details, and lessons learned are shared with the other entities.
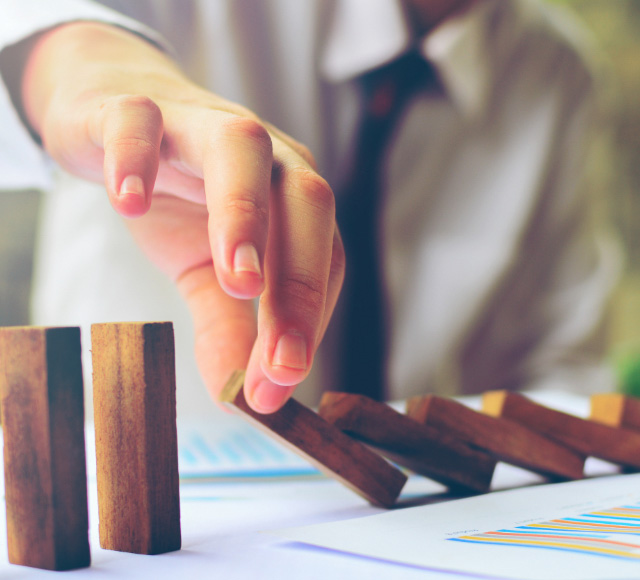