Product Stewardship
Product Stewardship at Indorama Ventures provides a framework for active engagement across the company to ensure that our products present no risk to health and the environment. It encourages innovation in our products and processes to meet increasing societal and business expectations regarding sustainability and transparency.
We identify risks and opportunities to reduce resource and material consumption through Life Cycle Assessments (LCA) of our products throughout the value chain. Furthermore, Product Stewardship and Innovation Management include an inter related set of business activities, policies and procedures, and organizational designs.
Our Product Stewardship initiatives include
Eco-design Criteria & Product Safety Communications
Our Product Design Criteria
Resources
(Renewable Energy, Water, carbon emissions)
Use Phase Impacts
Toxicity
Bio-based
(Recyclability Potential)
Biodegradability & Composability
Light weighing & Down gauging
Regulatory Compliances
(FDA, REACH, SIN list, SVHC list)
Transportation Efficiency
End of Life Management
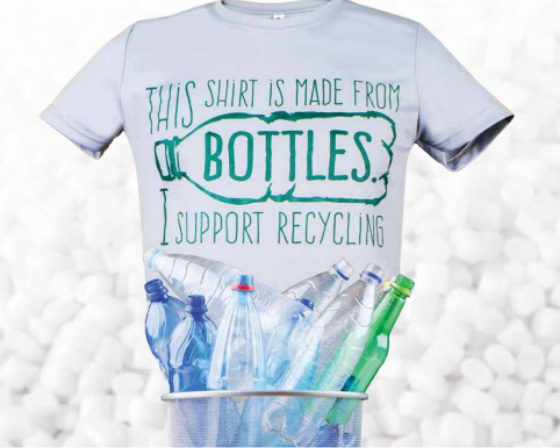
Indorama Ventures has implemented numerous process efficiencies that have resulted in dramatic efficiencies (measured by energy, GHG/ton of production). As Indorama Ventures seeks further efficiency gains, eco-design criteria evaluation and decision-making will be more formalized throughout the entire organization as part of our global Product Stewardship standard.
Indorama Ventures provides Safety Datasheets in GHS SDS format to customers. GHS formatted product labels are complete. Indorama Ventures, in keeping with Product Stewardship and Sustainability Leadership best practices, will begin the process of making these product safety communications more readily available through the company websites. This pro-active disclosure is in-line with the expectations of our customers and stakeholders, as well as leading initiatives such as Responsible Care.
Renewable Sourcing and Bio-based Feedstocks
Indorama Ventures is active in research and development projects aimed at using bio-based feedstocks for chemical products. Renewable raw materials and chemicals from bio-based content that we procure and use in our manufacturing needs to be certified (certifications must be provided) as originating from sustainable or environmentally friendly sources.
In order to realize greater acceptance and growth of these renewable alternatives, a number of current challenges -- such as scaling up the new technologies to achieve commercialization, staying on top of new technologies, as well as ensuring dynamic portfolio technologies and relationships -- will require continued innovation and deepened partnerships between Brand Owners, resin producers and others in the PET supply and value chain. The current confidential nature of these collaborations prohibits greater disclosure.
Indorama Ventures GMO Statement
Circular Feedstock Commitment
Bio-based feedstock: 16% against Indorama Ventures external feedstock
Recycled feedstock (Post-consumer PET bale input): 23% against Indorama Ventures PET feedstock by 2030
2024 Progress
Bio-based feedstock: 1.50% against Indorama Ventures external feedstock
Recycled feedstock (Post-consumer PET bale input): 4.94% against Indorama Ventures PET feedstock
Sustainable Pillow Made from Biopolymers PLA Feeling
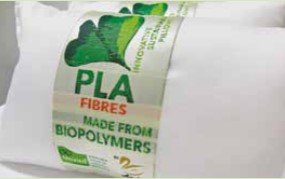
The filling for the pillow consists of 95% biopolymer PLA made from sustainable raw materials offer a sustainable alternative to petroleum-based fibers, in addition to being recyclable and 100% biodegradable with industrial composting. This pillow has qualified for our Sinfineco brand, which is only awarded to sustainable Trevira products.
AEROPOWDER – biodegradable insulating material
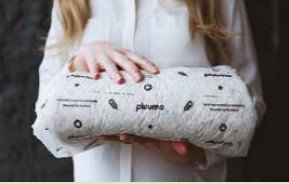
This productive collaboration between Trevira and AEROPOWDER resulted in the creation of a completely biodegradable insulating material. A start-up based in London launched a new sustainable product called pluumo – a biodegradable, innovative packaging material that harnesses the power of feathers. Feathers have naturally insulating properties, and to find a fiber that would help realize their design idea, AEROPOWDER turned to Trevira GmbH. We developed special binding fibers – bicomponent fibers consisting of two different biopolymers.
Substances of Very High Concern
As part of Indorama Ventures’s global Product Stewardship program, Indorama Ventures will maintain its own Restricted Substances List while developing a “Beyond Restricted Substances” list where the company will seek alternatives to these substances. These substances may not be directly regulated today, but as there is sufficient concern among stakeholders, Indorama Ventures will be proactive in monitoring and seeking alternatives.
The Product Compliance Risk Characterization (PCRC) process undertaken for 100% of our products is the mechanism by which this assessment is performed for their potential impact on human health and the environment. Specifically, the PCRC process gathers inputs from those interfacing with customers to obtain information about intended downstream applications. What follows is an assessment of each raw material with a focus on potentially new formulation components along with their effects on both manufacturing hazards and product compliance (in terms of both chemical registration and food safety) in target markets.
We evaluate chemicals used in our operations and their exposure to our employees and the environment, and have effective control of volatile substances on the SVHC list and SIN list that may present a risk.
We take a proactive approach, actively engaging in assessments and ensuring that we meet the European Union’s REACH regulations and other compliance requirements.
We comply with the ECHA SVHC list and are proactively removing products on the SIN list.
Our goal is to complete the comprehensive assessment of our raw materials, chemicals, and products during 2020 regarding the SIN list and to set a target for improvements by 2021. We monitor the release of SVHC updates and assess our raw material streams. In some cases, a substance could be on an SVHC list in raw form, but once it is converted to a different, benign form, it no longer has a product safety risk.
“Indorama Ventures is targeting zero violations against domestic and international regulations as well as zero use of any substance of very high concern (SVHC).” We evaluate the chemicals used in our operations and their exposure to our employees and the environment, with effective controls in place of volatile substances on the SVHC list and the Substitute it Now (SIN) list that may present a risk.
Indorama Ventures’ Hazardous Chemicals Commitment
Indorama Ventures' revenue in 2024
Highlights
- 100% of European entities were compliant with REACH regulations
- 100% compliance with the ECHA SVHC list
- Zero violations of domestic and international regulations
Case Studies:
Antimony-free flame retardant staple fibers
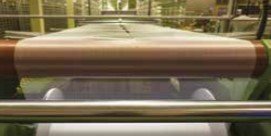
An important functional fiber which we produce is Trevira CS® , the world’s premier flame-retardant fiber. Trevira has extended the antimony-free technology to these fibers.
A new star has joined the Indorama Ventures family: Heavy Metal-Free iCareTM
iCareTM symbolizes the fifth core value of Indorama Ventures: “We are responsible”, demonstrating our industry leadership, sustainability, innovation, passion for excellence, eco-friendliness and a commitment to the success of our customers. Today, Indorama Ventures has the capability of supplying a whole range of iCareTM fibers, filament yarns and PET resins for the apparel, home care, hygiene, automotive sectors, and industrial applications. iCareTM staple fibers include, but are not limited to, 100% PET fine and coarse deniers, hollow conjugated, and bicomponent fibers for various downstream products including clothing, disposable hygiene, pillows and bedding, toys, automotive nonwovens, and industrial nonwovens. iCareTM PET filament yarns include partially oriented yarns, draw textured yarns, fully oriented yarns, colored yarns and differential shrinkage yarns. Indorama Ventures also offers iCareTM Heavy Metal Free Chips (resin) for filament yarns, spunbond/spunmelt and other products.
Product Sustainability Assessment (PSA)
Our Product Sustainability Assessment (PSA) methodology is based on WBCSD principles by design while the LCA is based on ISO 14040 and 14044.
As part of our strategy to develop more sustainable products in line with the needs of our clients and society, we developed a methodology that follows best market practices and which is based on the guidelines of the the World Business Council for Sustainable Development's Portfolio Sustainability Assessment (PSA).
In 2021, we analyzed the sustainability performance of strategic products in our existing portfolio for the HPC, CROP, Coating, and Oil & Gas segments, to learn about their respective strengths and implement action plans that improve those classified as underperforming. The methodology and internal evaluation process were audited and validated by a third party. The methodology was also adapted for products in development in 2021. The purpose of this action is to ensure that Oxiteno’s current product portfolio is always updated with developments duly classified under sustainability, while also making it possible to monitor the project portfolio and respective solutions being developed in this regard. This initiative will give us clear visibility in how well new developments adhere to Oxiteno’s sustainability strategies and expand management's capacity over the company’s solutions portfolio.
The PSA assessment is made through a qualitative and quantitative questionnaire composed of 26 environmental, social, and economic criteria, which analyze the product being applied at different stages of its life – from intrinsic characteristics, the manufacturing process, and use of the product by our client or even by an end user. Depending on the level of performance, the product must have an action plan for the adoption of control measures or, in terms of a positive evaluation, to leverage its sales.
Also, as part of the strategy for more sustainable products, Oxiteno measures the environmental impacts of its products and processes through Life Cycle Assessments (LCAs), a methodology governed by the ISO 14040 and 14044 standards, which quantifies environmental impacts – from the extraction of raw materials to the manufacturing and distribution stages, to use and final disposal. The results of the analysis can help the company make decisions regarding the choice of technological routes and raw materials with less impacts.
The 2030 sustainability strategic plan dedicated to the IOD business segment has a public target in which 15% of business revenues come from more sustainable products with 50% of new developments using the PSA and LCA methodology as a basis beginning in 2025.
Life Cycle Assessment (LCA)
Life Cycle Assessment (LCA) is a systematic analysis of product life cycle to assess the environmental impact from these products, by taken into an account of raw material acquisition to the end of their products’ life at disposal or recycle stage. At each stage of product manufacture, analysis of environmental impact is carried out by consideration of energy consumption, water consumption, air emission, waste water discharge, etc. that had been used for production of one functional unit.
Indorama Ventures’s journey towards LCA
As part of our sustainability efforts, Indorama Ventures monitors the effect of our products on the environment by conducting Life Cycle Assessment (LCA).
The reasons for LCA study is to “Quantify the various environmental impacts of the products to be used in the product stewardship program of the company for communicating to the stakeholders”.
Our main product is Polyethylene Terephthalate (PET), which is considered as an environmentally friendly polymer with no concerns to safety during its manufacturing process and use. PET is replacing glass, PVC and Polystyrene and is widely used in food and drink packaging. PET is also the main polymer used in synthetic fibers for textiles, with no adverse concerns to the consumers. PET is the only polymer that is recycled in a closed loop to food packaging or textiles.
Highlights of Products done LCA
Indorama Ventures has carried out LCA studies for its PET products i.e. Preform, Fibers- Yarn, fabric, wool, Recycled Flake, PET, PIA and PTA and Wool. and understands the impact on the environment during the manufacturing. Together with Industry partners Indorama Ventures is assessing the LCA of the use of PET including recycling.
Indorama Ventures worked with the University of Utrecht in the Netherlands in order to understand the carbon footprint of PET, to assess its environmental aspects and any potential impacts associated with a product and process. The analysis examined our plants in the Netherlands, Lithuania and Poland. The study concluded that the Indorama Ventures PET plants perform much better than the European average concerning CO2 emissions.
In addition, AlphaPet, one of our wholly-owned subsidiaries in the US, also carried out a Life Cycle Assessment in 2015. The report suggested that the contribution of global warming potential (GWP) of PET manufacturing at the AlphaPet site is comparable to the published literature data.
The Fibers segment conducted LCA studies of >90% products (by volume) produced in Asia in 2017. During 2019 these LCA studies will be revalidated by comparing results across sites and implementing learnings. Other sites, notably Wellman International (for its rPET) and Trevira, have also completed LCA. In all cases, these are to ISO standards and cover cradle to factory gate analysis.
We completed LCAs at all of our plants in Asia (excluding new acquisitions from 2017-2019) in accordance with ISO 14040/44:2006, with plans to extend LCAs to the rest of our operations.
The exercise will help Indorama Ventures to understand the various environmental impacts of the selected products which will then further be used in the product stewardship program of the company for communicating to the stakeholders.
Life Cycle Management (LCM)
It is the proactive and systematic management of information gained through the LCA that improves decision making. As a result of LCM, Indorama Ventures is able to more accurately identify cost reductions, process improvements, reduce risks and make strategic product decisions. We intend to commence LCM in all (relevant) Indorama Ventures operations by 2020.
Beyond Compliance
Indorama Ventures is ensuring full compliance of its products with all applicable legislation and local regulations. Indorama Ventures operations start at a baseline of a low chemical toxicity footprint. In order to promote best practice and industry leadership, Indorama Ventures has a system of benchmarking all its productions sites and is committed to further reducing potential toxicity in all its products.
Indorama Ventures is leading several industry organizations aimed at identifying new concerns related to the use of its monomers, additives and the use of the final product in sensitive applications such as packaging of food, pharmaceutical products and drugs. Indorama Ventures monitors all of the international environmental regulations and takes appropriate action, if necessary, to ensure that each of its products remains in compliance with all established toxicity threshold limits.
Indorama Ventures is identifying potential restrictions to the use of its monomers, manufacturing processes and final products and has a system to work with industry organizations to address these concerns in an early stage and avoiding that they result in legislative restrictions.
With regard to chemicals and their safe use REACH is one of the most important European Community Regulations. The aim of REACH is to enhance the protection of human health and the environment through the better and earlier identification of the intrinsic properties of chemical substances and by applying appropriate safety assessment and risk management for the use of those substances. Indorama Ventures met all the 2010 and 2013 REACH deadlines. Our REACH statements can be provided by the regional sales organization.
Our commitment
Lowering our overall environmental impact includes a target of 100% Energy and Environmental Management Systems in all our operations by 2020, and achieving 100% compliance of the European Union’s REACH regulation by 2018.
EU Member States Competent Authorities or the European Chemical Agency, may prepare dossiers for the identification of substances of very high concern. The outcome of this identification procedure is a list of substances that may be restricted or completely forbidden in the future. Indorama Ventures affirms that it does not intentionally add substances of very high concern or that its products contain these in concentration amounts above 0.1% weight.
Highlights
- 100% of European entities are compliant with REACH regulations
- 100% compliance with the ECHA SVHC list and proactively removing products on the SIN list Indorama Ventures is not listed as a manufacturer of chemicals on the SIN list
PLA filament yarns obtained ISEGA certification
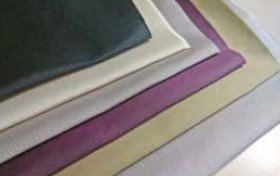
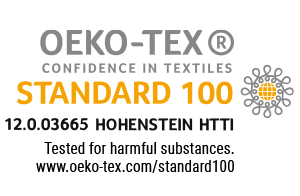
Flame retardant Trevira fiber and filament yarns are certified to STANDARD 100 by OEKO-TEX® and have been awarded its highest rating, meaning that they are suitable for baby and toddler articles.
STANDARD 100 by OEKO-TEX® is one of the world's best-known labels for textiles tested for harmful substances. It stands for customer confidence and high product safety.
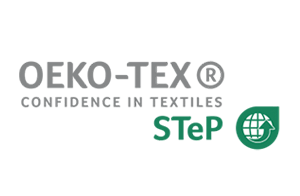
Also, our fiber products at Indorama Polychem Indonesia received the Oeko-Tex STeP certification.
STeP by OEKO-TEX® stands for Sustainable Textile & Leather Production and is a modular certification system for production facilities in the textile and leather industry for environmentally friendly and socially responsible production facilities along supply chain.
Find out here what STANDARD 100 means and why it is worth checking for this label when buying textiles at https://www.oeko-tex.com/en/
Product Toxicity
While our products are not harmful and compliant with all relevant regulations, we are always seeking ways to lower the potential environmental impact and toxicity of the raw materials and other chemicals used in our processes. We stringently monitor our raw materials, and any potential issue that is discovered is actively replaced with known, registered materials or with alternatives that are safe based on their chemistry. We evaluate chemicals used in our operations and their exposure to our employees and the environment, and have effective control of volatile substances on the SVHC list and SIN list that may present a risk.
We take a proactive approach, actively engaging in assessments and ensuring that we meet the European Union’s REACH regulations and other compliance requirements.
We comply with the ECHA SVHC list and are proactively removing products on the SIN list. It should be noted that Indorama Ventures is not listed as a manufacturer of chemicals on the SIN list.
Our goal is to complete the comprehensive assessment of our raw materials, chemicals, and products during 2020 regarding the SIN list and to set a target for improvements by 2021. We monitor the release of SVHC updates and assess our raw material streams. In some cases, a substance could be on an SVHC list in raw form, but once it is converted to a different, benign form, it no longer has a product safety risk.
“Indorama Ventures is targeting zero violations against domestic and international regulations as well as zero use of any substance of very high concern (SVHC).” We evaluate the chemicals used in our operations and their exposure to our employees and the environment, with effective controls in place of volatile substances on the SVHC list and the Substitute it Now (SIN) list that may present a risk.
The Product Compliance Risk Characterization (PCRC) process undertaken for 100% of our products is the mechanism by which this assessment is performed for their potential impact on human health and the environment. Specifically, the PCRC process gathers inputs from those interfacing with customers to obtain information about intended downstream applications. What follows is an assessment of each raw material with a focus on potentially new formulation components along with their effects on both manufacturing hazards and product compliance (in terms of both chemical registration and food safety) in target markets.
Product and substance testing and monitoring
We test when required to do so by law. We also test when we need data to complete a product risk assessment to our satisfaction, which is driven by the intended use(s) of the product and the exposure scenarios that are associated with their intended use(s).
For example, consider an Indorama product that is intended for use as a formulation aid in an agricultural product, that will be applied on to agricultural soil and crops that will be subsequently consumed by people. The biodegradation rate in surface waters – rivers, lakes – is important in case of a spill, or runoff from the land. The potential toxicity to living organisms in natural waters should also be considered. The biodegradation rate of the product in agricultural soil is an important data point, as is the potential toxicity of the product to organisms that live in these soils. The migration rate of the product in the soil is also important, because it is a key factor in determining how far a product might migrate before it completely biodegrades. Transportation workers, emergency response personnel, workers in our own operations, in the customers’ operations and in the field may be exposed to the product through the skin and eye – in case of an accidental splash – therefore, mildness to the skin and eye, and the product’s potential in causing skin sensitization (allergic reactions) are important data points. Skin irritation/corrosion must also be determined in order to assess whether the product is a dangerous good during transport. Our risk assessment approach aims to proactively assess each new product, for all relevant endpoints, before it is introduced into commerce.
Animal Testing
Indorama’s EHS group uses various tools to replace animal studies when possible, such as read-across approaches, weight-of-evidence arguments, in silico modeling and in vitro testing where available and appropriate. When a replacement for an animal study is not possible, various approaches are then used to combine study types to reduce animal numbers, such as a repeated-dose study plus a reproductive study, maximizing the study data generated by including additional parameters to reduce the potential of future studies, or alleviating stress when possible, so as to not to obscure vital endpoints.
Each of the laboratories Indorama contracts for animal studies are accredited by the Association for Assessment and Accreditation of Laboratory Animal Care International (AAALAC), adhere to Institutional Animal Care and Use Committee (IACUC) conduct and practices and include environmental and behavioral enrichment specialists, properly trained technical staff in animal care and husbandry, staff veterinarians and veterinary technicians.
Indorama’s EHS group plans to audit each of the laboratories conducting animal work on a regular basis once restrictions due to the pandemic have been lifted nationally/globally.